au sommaire
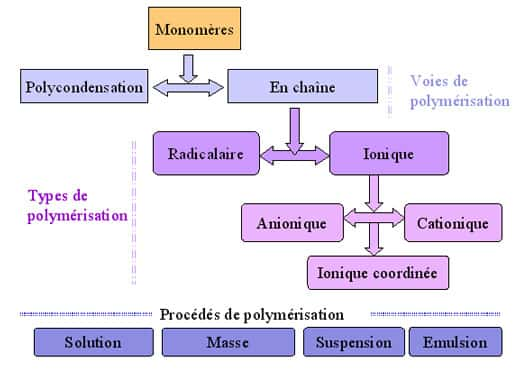
La polymérisation : Les méthodes de polymérisation et applications
Il existe deux grandes voies de polymérisation : la polymérisation en chaîne et la polycondensation.
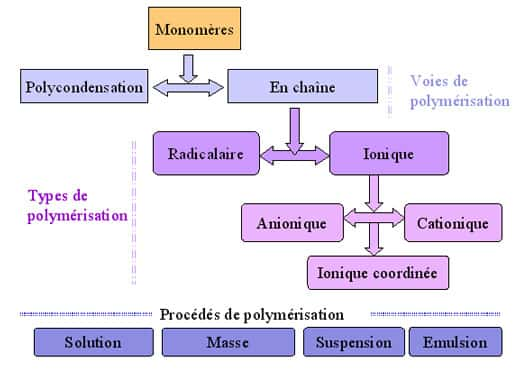
Voies, types et procédés de polymérisation.
1 - La polycondensation
La polycondensation est également désignée par le terme « polymérisation par étapes ». La formation de la macromolécule se fait par des réactions de condensation successives entre les fonctions chimiques des monomèresmonomères di ou polyfonctionnels. Ces réactions s'accompagnent généralement de l'élimination de petites molécules telles que H2O, fonction des monomères en présence. Dans cette voie de polymérisation, la chaîne grossit soit par addition de monomères, soit par additions d'oligomères. Cette polymérisation est longue et peut durer plusieurs heures.
L'un des polycondensats les plus connus est le PETPET : PolyEthylèneTérephtalate qui fait partie de la famille des polyesters. Il est obtenu à partir de diméthyl térephtalate (DMTP) et d'éthane1,2-diol (ou éthylèneéthylène glycol).
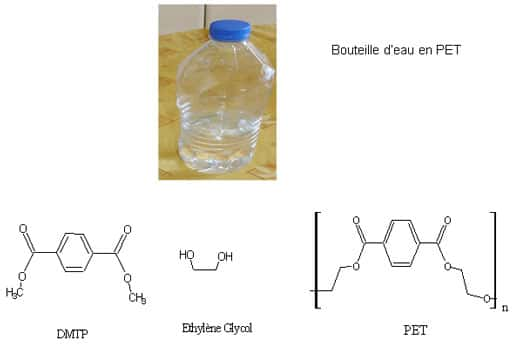
En raison de sa faible perméabilité aux gazgaz, le PET est très utilisé comme contenant de liquidesliquides alimentaires. Il peut être recyclé sous forme de fibres(fibres textiles à base de PET dans les polaires) ou sous forme de contenants.
Les polyamidespolyamides (NylonNylon ®), les polyesters, les siliconessilicones, et les Polyuréthanes sont également obtenus par polycondensation.
L'utilisation de monomères polyfonctionnels conduit à des systèmes tridimensionnels. La bakélite, obtenue à partir de phénol et de formaldéhydeformaldéhyde est un polymèrepolymère tridimensionnel. Ce polymère est un bon isolant thermique utilisé comme supports de circuits imprimés, queues de casseroles ...
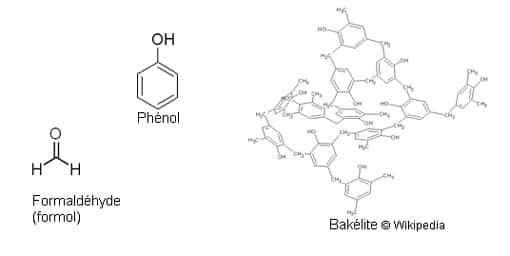
La réticulationréticulation des résines époxyépoxy par des durcisseurs (diamines aromatiquesaromatiques par exemple) conduit à un polymère thermodurcissablepolymère thermodurcissable dont les composites élaborés avec des fibres de verre sont utilisés comme matériaumatériau constitutif des coques de bateaux ultra légères. Certaines coques de bateaux sont en polyesters. La condensation de l'urée avec du formol donne une résine formant un réseau tridimensionnel serré, utilisée comme colle à boisbois et dans les panneaux de particules.
2 - La polymérisation en chaîne
Les réactions en chaîneréactions en chaîne font intervenir un nombre réduit de centres actifscentres actifs mais ces derniers sont très réactifsréactifs. Il s'établit entre 1000 et 10000 réactions primaires pendant la duréedurée de vie d'un radical (0.1 seconde)
Les réactions en chaîne se déroulent suivant 3 grandes étapes :
• L'amorçage qui conduit à la formation du premier centre actif.
• La propagation pendant laquelle les macromolécules croissent.
• La terminaison qui correspond à l'arrêt de la croissance des chaînes.
Les terminaisons déterminent la taille des chaînes. En polymérisation radicalaire, cette terminaison se fait par la réaction de deux radicaux macromoléculaires. Cette réaction peut être soit une addition conduisant à une très longue chaîne macromoléculaire soit une dismutationdismutation conduisant à deux chaînes macromoléculaires l'une contenant une fin de chaîne saturée et l'autre contenant une fin de chaîne insaturée.
La polymérisation en chaîne regroupe la polymérisation radicalaire et la polymérisation ionique. Cette dernière peut être anionique, cationique ou ionique coordinée. La polymérisation ionique coordinée se fait en présence de catalyseurscatalyseurs régiosélectifsrégiosélectifs de type Ziegler et Natta (prix Nobel partagé de chimiechimie 1963) à base d'halogénures de métauxmétaux de transition. Elle permet le contrôle de la structure moléculaire des polymères et permet l'obtention de polymères de très hautes masses molairesmasses molaires.
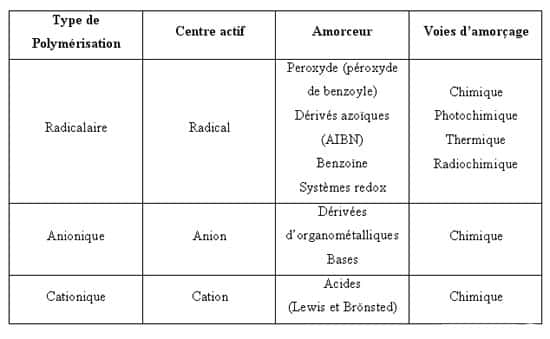
L'amorçage radicalaire se fait par rupture homolytique d'une liaison ( -O-O- dans les péroxydes par exemple).
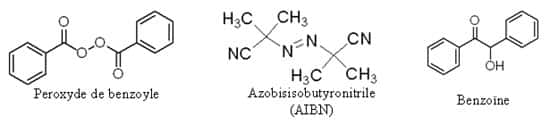
Les matériaux obtenus par polymérisation ionique ont une structure et des caractéristiques mieux contrôlées que celles des matériaux obtenus lors des polymérisations radicalaires. Les réactions de polymérisation ioniques sont plus rapides du fait du nombre important de centres actifs.
L'orientation vers une polymérisation anionique, cationique ou radicalaire est fonction du caractère électro-donneur ou électro-attracteur des substituants du groupement fonctionnel, de l'encombrement stérique et des possibilités de stabilisation par mésomériemésomérie du centre actif créé. Un polymère donné peut être obtenu suivant différents types de polymérisations mais les caractéristiques du matériau final seront fonction du type de polymérisation choisi. Ainsi, le PolyéthylènePolyéthylène (PE) produit par voie radicalaire est fortement ramifié (basse densité) alors que le PE produit par polymérisation ionique coordinée est linéaire et possède une masse Mn très élevée (haute densité).
Parmi les polymères d'usage courant obtenus par polymérisation radicalaire, on peut citer le polychlorure de vinylepolychlorure de vinyle (PVC) obtenu à partir du chlorure de vinyle, le Polytétrafluoroéthylène (PTFE, TéflonTéflon®), le polystyrènepolystyrène (PS) obtenu à partir du styrène et certains copolymères de styrène et de diènes.
L'un des polymères d'importance également obtenu par voie radicalaire est le polyméthacrylate de méthylepolyméthacrylate de méthyle (PMMA) obtenu par homopolymérisation du Méthacrylate de Méthyle.
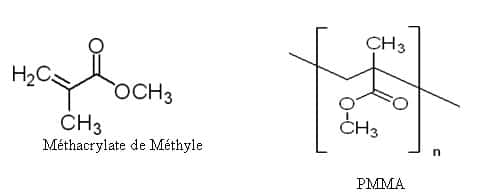
Le PMMA est un matériau rigide possédant d'excellentes qualités optiques. Il est entre autres utilisé pour les prothèsesprothèses dentaires, les cristallins artificiels, les enseignes, les meubles design, les accessoires de sécurité, les biberons...etc. Il est également connu sous les appellations Plexiglas ®, Altuglas ®, Lucite ® ou simplement verre acrylique.
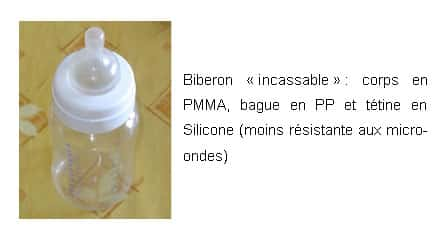
Les premières lentilles de contactlentilles de contact étaient élaborées en PMMA. Toutefois, la rigiditérigidité du matériau les rendait impropres à leur usage (irritation, faible perméabilité aux gaz). Le PMMA a donc été remplacé dans un premier temps par des copolymères PMMA-Silicone pour des lentilles semi-rigides perméables aux gaz. Les lentilles souples sont faites à partir d'hydrogelshydrogels de poly(méthacrylate de 2-hydroxyéthyle) réticulé (PHEMA). Ce dernier, grâce au groupement hydroxyle et à la réticulation avec du diméthacrylate d'éthylène glycol est hydrophilehydrophile sans être soluble. Ce matériau aurait une faible tenue mécanique en l'absence de réticulation.
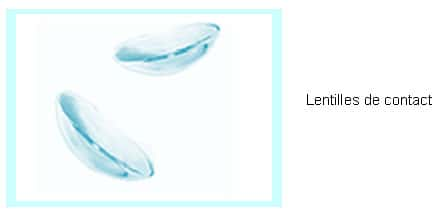
Le PMMA peut être refondu et remoulé. Il peut également être dépolymérisé à chaud pour la synthèse d'un nouveau polymère.
Parmi les polymères obtenus par voie ionique, on peut citer entre autres le PS, les polydiènes et les polymères obtenus à partir de dialkyl oléfines ( -CH2-C(R1R2)-n, R1 et R2 sont des groupements alkyls).
Les élastomèresélastomères synthétiques sont obtenus par polymérisation ionique coordinée (EPR, EPDMEPDM..). L'élastomère le plus connu est le caoutchouccaoutchouc naturel. Les élastomères sont appréciés pour leur grande incompressibilité, leur grande déformabilité et leurs caractéristiques rebond. Ainsi, les élastomères synthétiques sont utilisés comme joints d'étanchéitéjoints d'étanchéité (silicone, acrylique), comme colle (polychloroprène plus connu sous le nom commercial néoprènenéoprène ®) ou comme absorbeurs de chocs. L'un de ces absorbeurs de choc est le SBR, un copolymère styrène-butadiène.
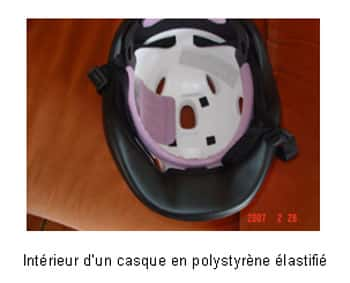
Les propriétés mécaniques des élastomères sont améliorées par la vulcanisationvulcanisation qui consiste à introduire un nombre raisonnable de ponts covalents entre les chaînes du polymère. Les pneumatiquespneumatiques sont composés d'un mélange de caoutchouc naturel, de caoutchouc synthétique, d'agents de vulcanisation ( contenant du soufresoufre), d'accélérateurs de vulcanisation, et d'additifs.
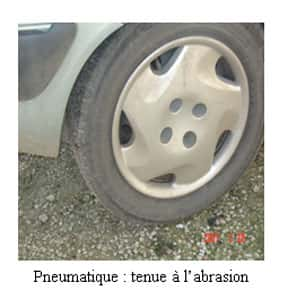
L'un des caoutchoucs synthétiques les plus utilisé est un copolymère Styrène-Butadiène comportant 15% molaires de styrène (SBR = Styrene-Butadiene Rubber).
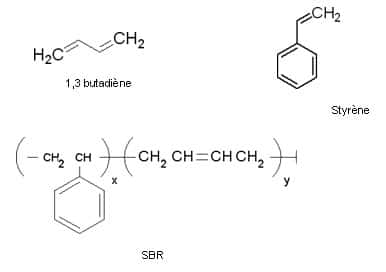
Les chambres à airair et le revêtement intérieur des pneumatiques tubeless initialement en caoutchouc butyle sont actuellement en caoutchouc butyle halogéné. Le caoutchouc butyle est obtenu par vulcanisation de polyisobutylène. Ce polyisobutylène est en réalité un copolymère statistique obtenu par polymérisation cationique d'isobutylène (98% molaires) et d'isoprèneisoprène (2% molaires).
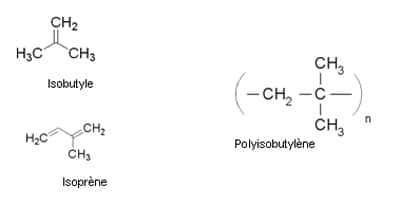
La présence d'isoprène dont il reste une double liaison après polymérisation permet la vulcanisation. Le caoutchouc butyle est environ 30 fois moins perméable que le caoutchouc naturel.